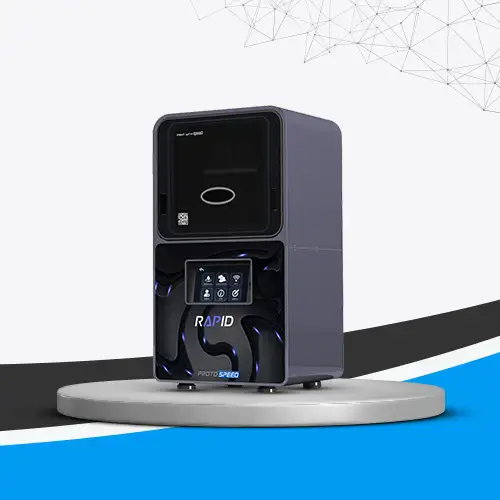
The Story of Protospeed
Our journey with 3D printing began in the year 2013, when 3D printers were starting to become commercialized. We had been manufacturing jewelry for many years, and with the utilization of the 3D printing technology available in the market, we witnessed a new era dawning upon the jewelry manufacturing industry. Initially, the 3D printing technology available in the market was notably expensive, slow in operation, and not easily accessible to many manufacturers. The photopolymeric materials that were available at that time presented numerous challenges, including frequent job failures and difficulties with castings.
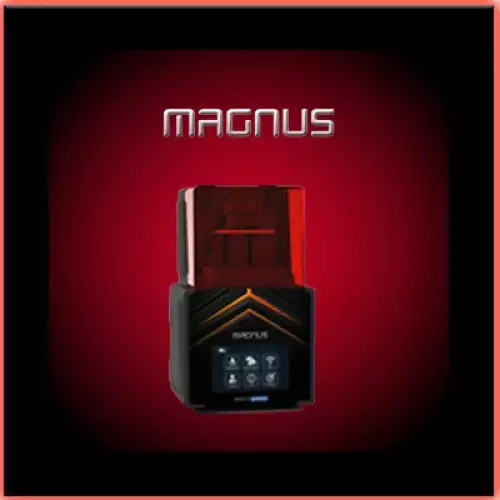
The Turning Point
The Turning Point The challenges mentioned earlier served as the catalyst for the concept of developing a 3D printer that could be accessible even to manufacturers at the grassroots level. This vision prompted us to establish a company equipped with a highly skilled R&D team. In 2013, we successfully engineered our inaugural 3D printer, which was subsequently made available to customers for beta testing. The outcomes yielded were truly remarkable. Yet, in alignment with the ever-evolving demands of the market, we discerned the impending significance of lightweight jewelry due to escalating gold prices. Simultaneously, a discernible shift was taking place in market trends, favoring the direct casting method while discarding the conventional die-making process. This paradigm shift ushered in a turning point for our journey.
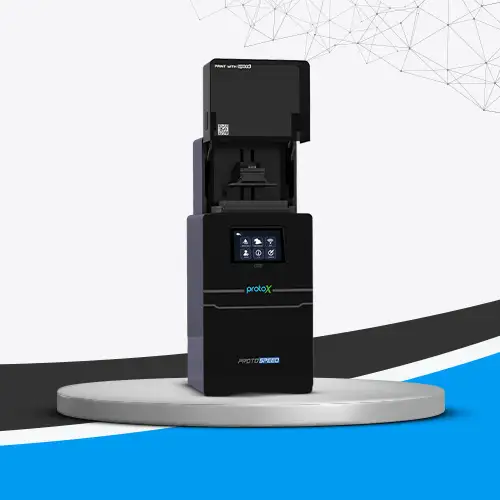
The Fast DLP
To meet the future market requirements, we worked day and night to invent a 3D printer that could deliver fast, cost-effective, and high-quality prints. In 2014, we completed our first 3D printer, which could print at speeds above 60mm/h. Later in 2014, we began selling this printer, and since then, there has been no looking back.
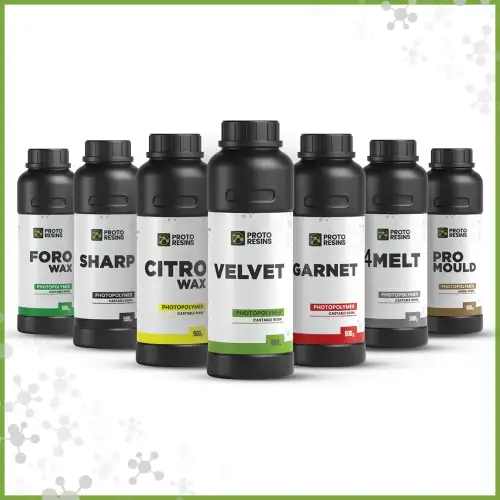
Resins
In pursuit of our mission to enable exceptionally fast 3D printing for direct casting, we required a supportive resin with qualities such as high precision, rapid printability, and ease of casting through a short burnout process. This endeavor led us to establish in-house resin production and R&D. Our ongoing commitment revolves around enhancing printing speeds and perfecting castability, driving us to continuously push the boundaries of innovation.