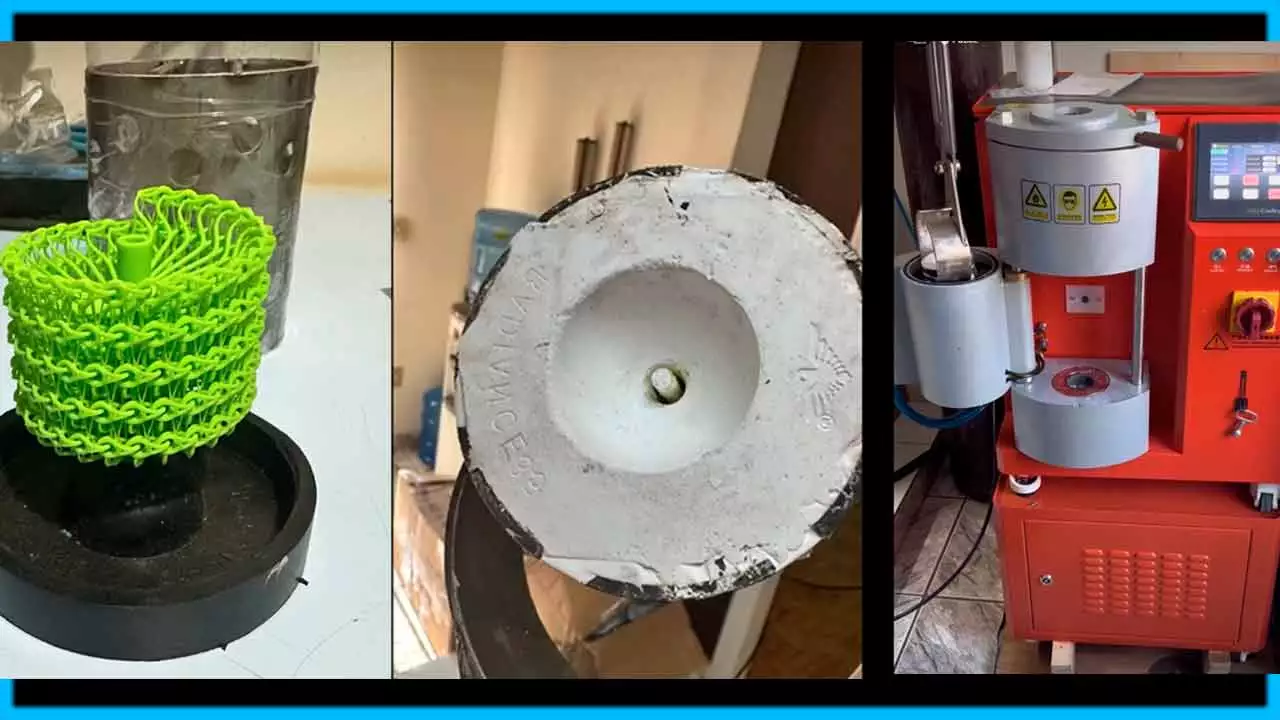
Best Resins for Jewelry Casting
https://protospeedfze.com/resins
Discover Castable ResinsJewellery Casting Step by Step Guide on the Process
Have you ever reflected on the enchanted journey of a piece of jewelry before it adorns your finger? It's an ancient art, perfected over millennia, transforming raw metal into exquisite ornamentation.
Throughout history, jewelry casting has remained a pivotal technique, melding timeless craftsmanship with evolving technology—a bridge between the artisan's vision and the tangible masterpiece you treasure.
Understanding Jewellery Casting
Jewellery casting, an infusion of science and alchemy, turns design dreams into wearable realities. It's a revered metamorphosis from molten metal to cherished heirlooms.
At its heart, jewellery casting involves precision and a dance with fire—melting metals into a liquid state are skillfully poured into custom-made molds. Each carefully crafted piece begins its journey veiled in the earth’s minerals, waiting to emerge as wearable art.
The term “investment casting,” another moniker for the process, speaks to the dedication required in each step. Engage with this art form; become part of its enduring legacy.
Defining the Casting Process
Jewelry casting is the mesmerizing transformation from liquid metal to solid adornment, capturing imagination in tangible form.
Every completed jewel began as a vision, cast in metal, reflecting a dream in every facet and curve.
This process marries ancient tradition with modern precision, creating pieces that speak of history while embracing the future, set within a design born from pure creativity.
Achieving this alchemy necessitates expertise, as precious metals are shaped by fire and skill into symbols of beauty and heritage.
Tools and Materials Needed
Before the alchemy begins, a well-equipped workspace is paramount. The crucible - your vessel for melting metals - awaits its fiery duties.
In this realm of transformation, specific tools for wax sculpting play the role of creators' first allies, shaping the dreams that will be encased in metal. The wax patterns, intricately carved or 3D printed, become the blueprint for what's to come. Flanking these are sprues and gates; channels guiding molten metal to its destination, ensuring perfection in form. They will be part of a tree-like structure, crucial for casting multiple pieces at once, maximizing both time and resources. Each tool is a promise of precision, a guarantee of artistic fidelity to the original design.
Precision strikes again as the investment powder, a refractory material, enters the scene, preparing to embrace the wax model in a heat-resistant shell. Mixed with water, it forms the investment slurry, which, once set, becomes the crucible's counterpart. It is an embrace from which the metal forms will be born, capturing every detail with devotion. This temporary forge needs flasks, sturdy containers that hold the investment and will later expose it to the heat necessary to liquify the wax.
At last, the heart of the process - the melting furnace. It cradles the crucible, heating the metal until it reaches a liquid state. Here, heat-resistant tools and safety gear are non-negotiable companions. Tongs, gloves, and face shields are your guardians in this dance with fire. The casting machine, whether a centrifugal or a vacuum assist, stands by to ensure the perfect flow of metal. Together, these elements form the symphony of craftsmanship, with each instrument critical to the breathtaking crescendo of a jewel's birth. They are the silent yet potent envoys of an age-old craft, beckoning new beauty into the world with every pour.
Casting Types and Methods
Lost-wax casting, also known as investment casting, is a star among jewelry-making techniques. Multi-step and intricate, it turns visions into heirloom wonders.
Since antiquity, artisans have innovated numerous methods, each with its temperament and expertise, such as sand casting for its rudimentary charm and elemental roots.
Centuries have refined methods like centrifugal casting, which harnesses centrifugal force to propel molten metal into the investment, ensuring even the most delicate designs materialize.
Vacuum casting, on the other hand, relies on atmospheric pressure to fill the mold. Its precision and ability to produce intricate pieces without porosity are unparalleled.
Delve into the realm of continuous casting for sheet and wire, which demands mastery, precision, and patience, ensuring quality and consistency in every creation.
Preparing the Original Model
The genesis of a treasured piece begins with crafting a flawless prototype. Carved with expert precision from wax or molded from metal, this master model embodies the eventual splendor of the finished jewel. Artisans must meticulously sculpt every curve and detail, as this template sets the standard for an entire series of breathtaking pieces.
This original harbinger is a testament to the artist's vision—a tangible draft where potential meets craftsmanship. It captures the essence of design and transforms abstract artistry into a blueprint for tangible beauty, making every minute invested in its perfection a promise of the exquisite pieces to come.
Designing Your Piece
Initiating the design process is akin to embarking on a journey of creation. Your imagination's spark ignites the path to a tangible masterpiece, distinct and resonant.
Envision the jewelry piece as a confluence of art and storytelling, where every curve, line, and detail embodies a narrative waiting to be adorned. It's not just an accessory; it's a vessel for expression, wrought from the whispers of your creative muse.
The design phase is about convergence—where functionality meets aesthetics. Consider the piece's wearability, comfort, and the interplay of its elements under the dance of light. How will it sit against the skin? How will it move?
In crafting your outline, you choose materials with intention, understanding how the various metals, gems, and textures will interact. Selection is key; only the finest materials ensure the piece's longevity, luster, and inherent value.
Remember, perfection in jewelry design isn't accidental. It's the culmination of thoughtful choices and a steady hand. It's where the possible is envisioned and the extraordinary begins to take shape.
Creating a Wax Model
Imagine the wax model as the jewelry's first breath of life—fragile yet foundational in the journey from concept to reality. This stage is where precision starts to take form, demanding an artisan’s unwavering focus and dexterity.
Crafting this wax prototype involves sculpting with meticulous attention to detail. From this embryonic replica emerges the intricate designs and features of the final piece. Here, every nuance is essential, every line a promise of the beauty that is to come.
Perfection in the wax model is non-negotiable; it serves as the master blueprint for the entire casting process. Skilled hands must balance artistry with the technical demands of casting, knowing that this model carries the DNA of the final jewel.
State-of-the-art tools and time-honored techniques converge to create a wax sculpture that is both precise and expressive. The slightest imperfection could propagate through to the metal casting, thus, the artisan’s touch must marry care with creativity.
This is the point of no return, where the physical form begins to echo the initial vision. The wax model is the critical vessel, holding the potential to become a piece that resonates with both maker and wearer.
Spruing and Gate System
In jewellery casting, creating a precise Spruing and Gate System is essential for the integrity and quality of the final piece.
1. Design the sprue to create a channel for molten metal to flow into the mold cavity.
2. Establish gate locations for strategically directing the molten material and aiding in the creation of multiple castings from a single pour.
3. Ensure proper thickness to facilitate the flow of metal and prevent premature solidification.
4. Optimize the sprue's placement on the wax model, which greatly affects the metal's flow and subsequent quality.
5. Calculate and implement sprue diameter while considering the metal type and casting size for efficient metal delivery.
6. Incorporate vents, if necessary, to allow gases to escape and avoid porosity in the casting.
The placement and design of sprues and gates significantly impact the metal's flow and final casting outcome.
By mastering the Spruing and Gate System, you not only avoid casting errors but ensure a level of craftsmanship that sets apart your jewellery as a piece of art.
Creating the Mold
In this vital stage, precision is paramount. An impression of the original wax model is captured in investment material, ensuring every exquisite detail is meticulously transferred. It's in this transition from wax to investment where the potential for extraordinary emerges, as the quality of your mold directly influences the delicate intricacies of your final jewel. The steadfastness of your craft here lays the foundation for irreplaceable magnificence.
Once the mold is set, it enters the critical burnout cycle, where it undergoes a high-temperature bake-out. This crucial step purges any remaining wax traces, leaving a perfect void that calls for the molten metal's embrace. Make no mistake, this perfect cavity is your artwork's crucible, poised to transform visionary design into tangible splendor.
Investing the Wax Model
Investing the wax model is a pivotal juncture in the creation of timeless jewelry, where meticulousness meets the melding of materials, leading to unparalleled results. It's a ceremony of transformation, inviting the permanent from the impermanent.
First, the wax replica is carefully secured within a flask. This dictates the eventual quality of the casting.
Next, a liquid investment compound is prepared—a precise blend of water and investment powder, ensuring no bubbles or inconsistencies that could mar the integrity of the future metal piece.
This mixture is then poured over the wax model inside the flask, encapsulating it entirely. It's a delicate dance of ensuring complete coverage while avoiding the introduction of air pockets. Attention to detail here is more than best practice—it's a sacred ritual that honors the design's complexity and ensures flawlessness in the final product.
Once the investment sets, we enter a realm where patience becomes virtue. The solidified investment block, housing the wax effigy, is gradually brought to high temperatures within the kiln. This phase is not merely a step; it's an ascension, a heralding in of the transformation that comes when voids left by vanished wax are filled with gleaming precious metal. As the wax departs, forming the negative space, anticipation builds; for here, in this negative, lies the promise of adding something truly extraordinary to the tangible world.
Burnout Cycle Essentials
The burnout process is a pivotal chapter in jewellery casting, where precise control of temperature and timing catalyzes the metamorphosis of wax into the void that will embrace molten metal. This is a meticulous ballet, where each degree and minute must be choreographed with uncompromising precision.
A kiln's caress must be gradual, avoiding thermal shock to the investment. Details matter, and patience is the guardian of quality.
Essentially, heating rates determine the thoroughness of wax elimination and mold integrity, ensuring that no remnants compromise the final casting (ensuring purity and accuracy).
Proper ventilation within the kiln cannot be overstressed. It's essential for evacuating the wax vapors cleanly, preventing defects that could tarnish the future jewel's brilliance.
Then begins the crucial soak at peak temperature, a purgatory for impurities where endurance of the mold is tested, ensuring that only the strongest survive to receive the molten blessing.
Ultimately, the cool down phase holds its own weight in this symphony of transformation. It's a period that allows the investment to stabilize, ensuring it's ready to cradle the liquid artistry that will soon flow into its embrace.
Testing Mold Integrity
Before pouring heart and soul into molten metal, mold integrity stands as the silent gatekeeper of quality. It's a fortress that must hold against the fiery siege, ensuring any design intricacy faithfully transitions from wax to wearable art.
Beneath the kiln's glaring stare, cracks and fissures are unacceptable. Their presence is the herald of failure and the antithesis of the jeweler's craft.
Vigilance in mold surveillance is akin to shoring up defenses before battle. Any weak spot (such as air pockets or incomplete curing) signals an immediate concern.
Stress tests must be conducted with the finesse of a surgeon. Probing the mold’s soundness, anticipating the stresses it will face, is a prerequisite to ensuring that what emerges is immaculate.
When the mold passes the baptism of stress tests, it's a moment of critical validation. This is where the alchemy of transformation is poised to weave precious metals into the legacy of lasting beauty.
However, it’s not just about passing these tests. Ensuring consistent excellence requires repeated verification under the harshest conditions to maintain the high standards we promise.
The Casting Operation
In the heart of the casting process lies the precision-driven task of turning molten metal into marvels of jewelry; this is the casting operation. It's a symphony of meticulous orchestration—where timing, temperature, and technique converge to create a flawless outcome. The molten metal is coaxed into the carefully crafted cavities of the mold, filling every nook and cranny with the promise of a masterpiece. As it surges into the mold, it is crucial that the metal flows unhindered, free of turbulence, to avoid the creation of air gaps or impurities that could mar the final piece. This complex ballet, where molten beauty meets rigorous control, requires the hand of a seasoned artisan and the eye of a perfectionist, ensuring that each pour is poised to manifest the jeweler’s vision into tangible treasures.
Melting and Pouring Metal
The crucible now becomes the cauldron of transformation, where metal transitions from solid to liquid. The chosen metal—silver, gold, or platinum—is placed within the crucible and subjected to intense heat. It is a pivotal moment where the air whispers anticipation and the future shape of beauty simmers in a molten pool.
Within the foundry's fiery embrace, the alloy's components merge, their atoms dancing in the heat until a shimmering liquid emerges. The metallurgist, a conductor of elements, tunes the temperature precisely, targeting the ideal melting point. This is a meticulous science, the cornerstone of the journey from raw material to intricate jewelry.
Temperature must be mastered; any deviation could spell disaster, forming flaws unseen until the final reveal. As the metal reaches its zenith of fluidity, the caster readies for the pour, a confluence of control and artistry. This step requires an unwavering focus, for the quality of the pour is synonymous with the quality of the final product.
With steady hands and years of expertise, our artisan initiates the pour. The molten metal cascades with purposeful grace into the mold, a moment where skill and science fuse. Any hesitation or miscalculation can introduce defects, challenging the integrity of the piece, yet the practiced pour is poetry in motion.
And thus, the metal finds its new form, settling within the confines of the mold's design. In its glowing descent, a nascent piece of jewelry is born, ready to be cooled, to solidify into a testament of craftsmanship and allure. This act, unseen to many, is the true genesis of finery, a narrative of fire, metal, and transformation.
Cooling and Mold Breakout
Once the molten metal is poured, it begins to descend from its peak temperature in a transformative journey towards solidity.
● The mold and its contents must cool uniformly to prevent stress and cracks.
● Time is crucial; cooling too quickly or too slowly can affect the metal’s integrity.
● It’s vital to monitor the temperature drop to ensure it aligns with material specifications.
● Patience is the companion of quality – allow the piece to solidify at its own pace.
Unveiling the metal’s final form is a meticulous task, as the mold is carefully broken away.
The successful blend of precision and patience becomes evident, revealing a creation that encapsulates both beauty and strength.
Cleaning and Finishing Techniques
After extraction from the mold, residual investment material clings to the metal, requiring removal to reveal the design's full potential. Initial cleaning is both a necessity and a pathway to perfection.
Meticulously, the piece undergoes a series of processes designed to eradicate any traces of the casting process. From water jets that remove investment particles, through to pickling in acid baths that eliminate oxidation, each step is deliberate. It's the bridge from rough casting to a piece artfully prepared for finishing touches, priming every surface for the artist’s final vision to take shape. Mindful techniques ensure that the integrity of the metal is preserved while it's gradually brought to a state of pristine condition.
Subsequently, finer details of the artwork emerge through precision polishing. Techniques such as tumbling with media, burnishing, and manual polishing with compounds are employed. Here, artisans practice their craft judiciously, their tools dancing over the metal to accentuate contours, enhance brilliance, and coax out the subtleties of the design. It is a process where technical skill meets aesthetic sensibility, resulting in a signature gleam that only high-quality jewelery possesses.
In culmination, quality control measures ensure that no flaw, however minute, eludes the vigilant eyes of the jeweler. Under magnification, every nuance is inspected, any blemishes are corrected, and reflective surfaces are reviewed to ensure a flawless finish. It's here that the jeweler's expertise truly shines, as they affirm the piece's readiness to join the pantheon of exquisite adornments. This meticulous attention to detail ensures that each piece not only meets but exceeds the expectations of those who seek nothing short of excellence