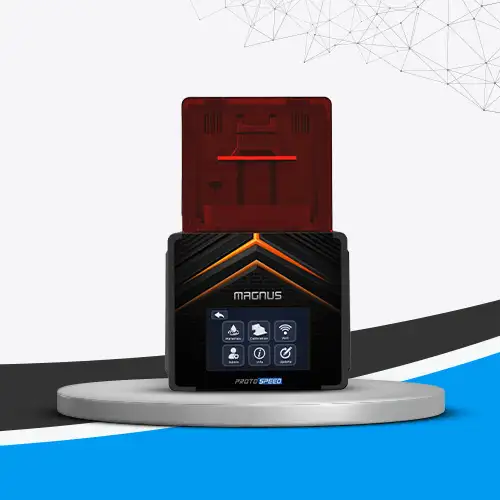
JEWELRY CASTING: A COMPREHENSIVE OVERVIEW OF THE PROCEDURE
Casting jewelry has always been a key method, combining ageless artistry with cutting-edge technology to create a link between the creator's vision and the tangible work of art you will cherish.
DISCOVER JEWELRY CASTINGJEWELRY CASTING: A COMPREHENSIVE OVERVIEW OF THE PROCEDURE
Have you ever considered the magical journey a piece of jewelry takes before it becomes a part of your finger? It's an old craft that has been refined over millennia, turning plain metal into beautiful decoration. Casting jewelry has always been a key method, combining ageless artistry with cutting-edge technology to create a link between the creator's vision and the tangible work of art you will cherish.
Comprehending Jewelry Casting
Through the use of science and alchemy, jewelry casting makes the visions of designers come to life. The transformation from molten metal to treasured keepsakes is a revered process. Jewelry casting is essentially a precise and fire-dancing process where metals are melted into a liquid and then expertly poured into specially designed molds. Every painstakingly made item starts covered in minerals from the ground and waits to become wearable art.
Establishing the Casting Procedure
The fascinating process of turning liquid metal into solid jewelry, or jewelry casting, translates creativity into physical art. Every finished jewel was once a vision that was cast in metal and each curve and facet reflected a dream. Through the marriage of age-old custom with contemporary accuracy, this method produces objects that embrace the future while speaking to the past, all contained within designs that are entirely creative in nature. Because precious metals are fashioned into symbols of beauty and legacy by fire and skill, achieving this alchemy requires competence.
Required Equipment and Supplies
It is essential to have a well-equipped workspace before the alchemy starts. Your metal melting vessel, the crucible, is ready for its intense tasks. Specialised wax sculpting tools shape the fantasies that will be wrapped in metal, acting as the first line of defence for artists. The elaborately carved or 3D printed wax patterns serve as a template for future developments. Sprues and gates surround them, serving as conduits to move molten metal to its intended location while guaranteeing form accuracy.
A refractory substance called investment powder appears and becomes ready to envelop the wax figure in a shell that can withstand heat. It is combined with water to create the investment slurry, which when solidified, becomes the crucible's opposite. It's an embrace that will give birth to the metal forms, meticulously catching every detail. The investment is held in flasks, which are strong containers that will subsequently be exposed to the heat required to liquefy the wax.
Finally, the melting furnace, the centre of the operation. It holds the crucible in place while heating the metal to a liquid state. Safety clothing and heat-resistant tools are essential companions in this situation. Your protectors in this fire dance are tongs, gloves, and face shields. Whether it is a centrifugal or vacuum assist casting machine, it is ready to guarantee the ideal metal flow. These components work together to create the symphony of craftsmanship, with each piece being essential to the amazing crescendo of a jewel's birth.
Casting Techniques and Types
Investing in jewelry is made possible by the popular lost-wax casting method. It is complex and multi-step, transforming visions into treasured marvels. Sand casting, with its simple appeal and elemental origins, is one of the many innovative techniques that artists have created throughout antiquity, each with its own temperament and skill set. Centuries have been devoted to perfecting techniques such as centrifugal casting, which uses centrifugal force to press molten metal into the investment, guaranteeing the realisation of even the most intricate designs. The filling of the mould in vacuum casting, however, depends on ambient pressure. It is unmatched in its accuracy and capacity to create complex objects without porosity. Explore the world of continuous casting for sheet and wire, which requires skill, patience, and accuracy to guarantee consistency and quality in each piece.
Establishing Up the Original Model
The creation of an impeccable prototype is the first step towards creating a valuable piece. This master model, which is either moulded from metal or expertly carved from wax, captures the ultimate beauty of the completed diamond. Artists have to carefully carve each curve and feature because this model serves as the model for a whole line of amazing sculptures. This unique harbinger, a physical draft where potential meets skill, is a tribute to the artist's vision. It embodies design and turns abstract art into a blueprint for measurable beauty, so every minute spent perfecting it is a guarantee of the magnificent works that will follow.
Crafting Your Work
Starting the design process is like starting a creative trip. The spark of your imagination lights the way to a tangible, unique, and poignant artwork. Imagine the jewelry item as a fusion of art and narrative, with each curve, line, and detail embodying a story just ready to be embellished. It's more than simply a piece of clothing; it's a medium for expression made from the inspiration of your inner artist.
The goal of the design phase is to bring usefulness and aesthetics together. Think of how comfortable and wearable the item is, and how the elements interact with the light as it dances. How is it going to feel on the skin? How is it going to move? You intentionally select the materials for your outline, taking into account the interactions between the different metals, jewels, and textures. The lifespan, lustre, and intrinsic value of a piece are guaranteed only by the finest materials, thus selection is essential.
How to Make a Wax Model?
Consider the wax model to be the jewelry's basic, fragile first breath during the concept-to-realm process. At this point, accuracy begins to take shape and calls for the constant attention to detail and dexterity of an artist. This wax prototype required painstaking attention to detail in its moulding. The complex characteristics and designs of the finished item are derived from this embryonic duplicate. Every detail matters in this situation, and every line portends future beauty.
Gate System and Spruing
For the integrity and calibre of the finished piece in jewelry casting, a precise Spruing and Gate System must be created.
• Create a channel in the sprue design so that molten metal can enter the mould cavity.
• Set up gate locations to help create many castings from a single pour by intelligently guiding the molten material.
• Make sure the thickness is appropriate to allow the metal to flow through and avoid early solidification.
• Place the sprue as optimally as possible on the wax model; this will have a big impact on the metal's flow and quality afterward.
• For effective metal delivery, compute and apply the sprue diameter while taking the casting size and metal type into account.
• If vents are required, include them to let gases out and prevent porosity in the casting.
• The final casting result and the flow of the metal are greatly influenced by the positioning and layout of sprues and gates. You may prevent casting faults and guarantee a degree of quality that distinguishes your jewelry as a work of art by becoming proficient with the Spruing and Gate System.